A client recently asked me what were some of the things I look for when assessing an equipment-related schedule for the first time. My frame of reference is drilling equipment, mostly well control equipment.
TIP #1: I’m immediately wary of any activity that takes longer than a week
Why? Mainly because I decided years ago that I don’t want to go longer than a week before finding out something is wrong. Short durations create a built-in early warning system where I can query the health of my project in a way that allows quick recovery if needed.
If you have any activity that is a week or less but you forgot to check status, the worst case is you’ve lost only one week if something went wrong a few days earlier.
Also, most people just aren’t that good when estimating activities longer than a week. It’s not a slight, it’s human nature. We’re better at seeing things on a shorter time horizon. People will tend to throw out large numbers without having thought through the sub-activities, people, parts and tools required. The longer the duration, the less clarity and the greater the risk.
Longer durations also require some uniform rules for people to report % complete. I’ve found that most % completes are pulled out of the ass. I’d rather eliminate the guesswork. Either you started or you didn’t. Either you finished or you didn’t. You can be binary like this when your activities are short.
So, how short? Coming from a product development/manufacturing background, I’ll take activities of one or two day duration whenever possible. Some activities will be place holders for long lead materials, but if you ask the right questions, you can usually get the vendor to break down their internal activities so that you can monitor their progress at least once during the week and not just take their word for it that they’re on track. After all, it’s your neck if they’re late.
In and around shipyards, I’ve found that there’s way too much going on to have activities (i.e. fab, machining, assembly, install, repair, etc) scheduled for more than a day (excluding waiting on parts).
Breaking activities down into sub-activities will force you to discuss those activities in detail. This will uncover hidden biases, traps, false assumptions and missing people, tools and parts. You’ll reduce project risk substantially. But also be aware that you’ll tie up your resources longer and this will likely require buy-in from the functional managers, client and vendors. But as the 1st Law of Thermodynamics states, you don’t ever get something for nothing. There’s likely going to be more pain up front, but it’s better when you’re in control from the beginning and not reacting to events later.
So, here is an example.
Notice in Figure 1 that activity 1.2 “Prepare for purge and pressure integrity test” is six days long. This activity is too long which means it’s too vague, with too much left to chance. It should be broken down into sub-activities.

Figure 1: WARNING! Activity 1.2 is longer than a week. Investigate!
See Figure 2 where activity 1.2 has now been broken down further into nine sub-activities. Notice that in this example, talking through the steps with the techs who will do the work actually reduced your overall project duration by two days. Don’t laugh, it happens. You now have plenty of verifiable opportunities to ensure that your project stays on track and your techs have a good checklist for what they’re about to do.
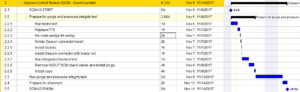
Figure 2: Activity 1.2 has been broken down into subtasks.
As a final note, one of my most successful projects was 12 months, consisting of four months of planning and eight months of execution. Yes, you read that right! One month of planning to every two months of execution!
Next week, I’ll discuss a tip for scheduling engineering work.
© 2017 by LinRich Solutions, LLC. All rights reserved