In a previous post, Frank emphasized the challenges of product development and the importance of pre-planning and having an A-Team involved.
We put his assertions to the test over the past 2 months by developing a product that allows a non-hazardous tool to be safely operated from a hazardous area. There was a blend of electrical, electronic and hydraulic engineering disciplines involved.
The breakdown of the Alpha prototype development is as follows.
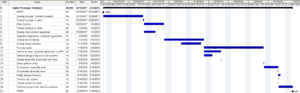
Alpha Prototype Schedule – Done in 2 Months
First, there were a few weeks of planning and working through the concept with the client. This was followed by due diligence which produced some commercial and contractual agreements with the client and our various independent contractors. Then there were about 2 weeks of engineering design done by a very experienced electrical engineer, followed by about 3 weeks of ordering and receiving parts. Then there were a few hours of planning work with a shop skilled at electronic and hydraulic assembly, followed by 3 days of assembly and test at the shop. Many of these activities overlapped.
Our mission for prototyping is to fail fast … design what we can and figure out the rest. I’d say the blend of shop work consisted of about 85% following the engineer’s design intent and about 15% free-wheeling in order to fill in the gaps left open (intentionally) by the engineer (by the way, good engineers know they don’t have all the answers as there is always some blend of practical considerations by the people who will build and maintain the equipment). We remembered to capture the practical input in the design.
As someone who continually harps on the value of planning everything out before spending a lot of money, I believe the work done by Frank, who invented the concept and worked out the human factors and what the system will do and why, was of paramount importance. Putting this all in writing was key. This document (called an OpsCon or operational concept) allowed us to commit to a scope with the client and enabled the engineer to design a solution and determine what components to use. But none of the development would have been successful if there wasn’t a highly competent shop team that could interpret the engineer’s intent while also having the ingenuity, skills and experience to ad-lib key aspects of the assembly work–frequent communication and a white board were absolute necessities here.
The Alpha prototype system was successfully field tested by the client and his customer approximately 2 months following his first phone call.
Next step is to implement some of the client’s suggestions for improvement in the Beta prototype, which is already underway. Then it will be on to production (and ROI).
If you have a product idea that you’d like to see through development, give us a call.