We have found that the best projects typically have sufficient planning up front. This has been accomplished with a handful of the right people, most of the time. This “A-Team” is typically diverse, with decades of experience. The team is capable of:
- understanding the issues
- developing an accurate problem statement
- developing product requirements; and
- accurately estimating what it’s really going to take.
Key quote: “major cost savings can be obtained by investing 5-15% of the projects resources in the early portion of the project”. (Design by Prototype, by Mulenburg and Gundo).
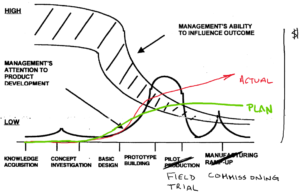
Figure 1: Management Attention During Product Development (Taken and Modified From Design by Prototype by Mulenburg and Gundo)
Note the graph above adapted from the same paper. The black lines represent senior management’s focus during the “common” development path of the “one-off” oilfield solution. The green line is a typical project plan that is usually developed right after the order is taken and the basic design (usually already late) is about to start. The red line represents the actual cost and time delays as the plan morphs into reality. Note that senior management might have mitigated the catastrophe earlier by focusing on proper up-front planning, but they usually only realize their mistake later as costs and time accumulate beyond expectations. Your results may vary, but this scenario can generate very animated discussions between senior management and the design and manufacturing teams, plus it can severely jeopardize the client’s goodwill. Typically, even with the soaring costs and delays, the project can’t be cancelled. So the effort necessary to finish the project and address the issues is much more expensive than it could have been if senior management had focused on proper up-front planning. It can be orders of magnitude cheaper to prevent than to cure.
Have a product development problem that needs an independent assessment to understand what it will take to turn the situation around? Call us, we can help.